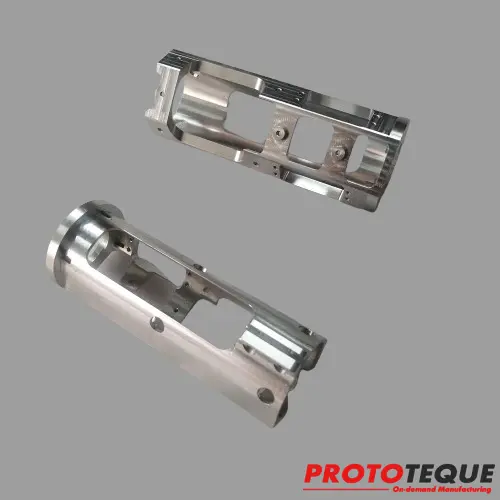
1、What is Aluminum Machining
Aluminum CNC machining involves using a CNC (Computer Numerical Control) machine, which operates based on a computer program. This process is used for both prototyping and full-scale production. Aluminum is a popular choice for machining because it is easy to work with and is widely used in manufacturing due to its excellent machinability.
2、Benefits of Using Aluminum for CNC Machining
Aluminum is a top choice for CNC machining across various industries due to its unique properties. Here’s a deeper look into why aluminum is favored for applications in automotive, aerospace, medical, and consumer electronics:
- Excellent Machinability
Aluminum’s soft and lightweight nature makes it one of the easiest metals to machine. This characteristic translates to faster cutting speeds, reduced tool wear, and minimal power requirements compared to harder metals like steel. The material’s ability to chip away easily ensures high precision and tight tolerances, leading to lower production costs and shorter lead times. The ease of machining allows for efficient production of complex and intricate parts. - High Strength-to-Weight Ratio
Aluminum is about one-third as dense as steel but maintains a high level of strength. This high strength-to-weight ratio is particularly valuable in industries where reducing weight is critical, such as aerospace and automotive sectors. Aluminum’s strength-to-weight ratio often outperforms that of stainless steel, making it a cost-effective alternative to more expensive materials like titanium while still delivering robust performance. - Corrosion Resistance
One of aluminum’s standout features is its natural corrosion resistance. When exposed to air, aluminum forms a protective oxide layer that prevents further oxidation. This layer is self-healing, which helps maintain the material’s integrity even if scratched. For enhanced durability, aluminum can be anodized, which not only boosts its corrosion resistance but also allows for a range of aesthetic finishes. Most commonly used aluminum grades provide excellent protection against environmental factors. - Performance in Low Temperatures
Unlike many metals that become brittle in cold conditions, aluminum retains its strength and ductility at low temperatures. This resilience makes it suitable for use in environments where other materials might fail, ensuring reliable performance in extreme conditions. - Electrical Conductivity
Aluminum is known for its high electrical conductivity, making it an ideal material for electrical components such as busbars and connectors. Although aluminum alloys may have slightly lower conductivity compared to pure aluminum, they still perform well in many electrical applications. This property is particularly useful in the manufacturing of components for electrical and thermal management systems. - Recyclability
Aluminum’s high recyclability is a significant advantage. Recycling aluminum uses much less energy compared to producing new material, making it a more sustainable choice. This not only reduces waste and conserves resources but also helps lower manufacturing costs. The ease of recycling supports environmentally-consciousprojects and contributes to cost savings. - Custom Finishing Options
Aluminum parts offer versatile finishing options to meet both aesthetic and functional requirements. Popular finishes include anodizing, which enhances durability and allows for various color options. These custom finishes improve the appearance and performance of aluminum parts, making them suitable for a wide range of applications. - Adaptability to Complex Designs
In my experience, one of aluminum’s greatest advantages is its adaptability to complex designs. The material’s machinability allows for intricate parts with detailed features, which is essential in fields like medical device manufacturing where precision is crucial. Aluminum’s ability to be easily shaped and refined makes it a versatile choice for applications requiring both complex geometry and high precision.
Overall, aluminum’s combination of machinability, strength, corrosion resistance, and recyclability makes it an excellent material for CNC machining. Its adaptability to complex designs and performance in various conditions further solidify its position as a preferred choice in many industries.
3、Where Does Aluminum Come From?
Aluminum is the most abundant metal in the Earth’s crust. It primarily comes from bauxite ore, which contains 30% to 60% aluminum oxide (alumina) along with other materials such as silica and iron oxides.
To transform alumina into aluminum metal, a two-step process is used:
- Alumina Extraction
Bauxite ore is processed to extract alumina, which involves crushing the ore and treating it to separate the alumina from impurities. - Smelting to Produce Aluminum
Alumina is then smelted through electrolysis, where it is dissolved in a fluorinated bath and subjected to an electrical current. This process separates the aluminum metal from oxygen. The resulting aluminum is collected, combined with recycled aluminum, and melted. It is then cast into various forms like sheets, billets, rods, and wires, which are further processed into finished products.
4、Aluminum Grades
Aluminum’s versatile properties make it a popular choice for many applications, including CNC machining. The right aluminum grade for your project depends on specific requirements, as each grade has distinct characteristics. Here’s an overview of common aluminum alloys by series:
- 1000 Series
These alloys are nearly pure aluminum, with about 99% aluminum content. They are very soft but can be hardened through mechanical processes. For example, aluminum 1050 is often used in applications requiring good corrosion resistance and high thermal conductivity, like heat exchangers and chemical processing equipment. - 2000 Series
Copper is the main alloying element in this series, which makes these alloys strong and capable of being heat-treated for further strength. Aluminum 2024, known for its high strength and good fatigue resistance, is commonly used in aerospace components like aircraft structures and automotive parts.
- 3000 Series
These alloys use manganese as the primary alloying element and are known for their excellent formability. Aluminum 3003 is widely used in products that need good corrosion resistance and easy machinability, such as kitchen utensils and beverage cans. - 4000 Series
Silicon is the major alloying element, resulting in alloys with a lower melting point. Aluminum 4045, for example, is used in automotive applications for heat exchangers and cladding due to its excellent thermal and mechanical properties. - 5000 Series
Magnesium is the primary alloying element here, giving these alloys excellent resistance to corrosion. Aluminum 5052 is often chosen for marine applications, including boat hulls and ship structures, because of its outstanding durability in harsh environments.
- 6000 Series
Silicon and magnesium are combined in this series, making these alloys versatile and heat-treatable. Aluminum 6061 is frequently used in structural applications like bridges and aircraft parts due to its good strength-to-weight ratio and resistance to corrosion. - 7000 Series
Zinc, along with elements like magnesium and copper, is the main alloying component, providing high strength through heat treatment. Aluminum 7075 is commonly used in aerospace and military applications, where high strength and resistance to stress corrosion are crucial. - 8000 Series
This series includes various alloys with different alloying elements like iron and lithium. For example, aluminum 8090, which contains lithium, is used in high-performance aerospace applications to reduce weight while maintaining strength.
5、Common Aluminum Grades and Their Uses
Aluminum is available in various grades, each designed for specific applications based on its properties. Here’s a guide to some of the most common aluminum alloys and where they’re used:
- Aluminum 2024-T3
Aluminum 2024 is renowned for its high strength and excellent fatigue resistance. It’s particularly valuable in the aerospace and defense sectors. Applications include:- Aircraft Wing Skins: Provides durability and strength.
- Armored Vehicles: Offers high resistance to stress and impact.
- Wheels: Used in both aviation and automotive industries for lightweight, strong wheels.
- Electronics Casings: Protects sensitive components with its strength and machinability.
- Aluminum 6063-T6
This grade is known for its good strength-to-weight ratio and corrosion resistance, along with ease of forming and welding. It’s commonly used in:- Lighting Fixtures: Offers an appealing finish and durability.
- Automotive Bumpers: Lightweight yet strong, perfect for collision protection.
- Power Distribution Systems: Reliable for electrical components and structures.
- Boat Frames: Combines strength and corrosion resistance for marine environments.
- Aircraft Components: Utilized in various parts for its ease of fabrication and resistance.
- Aluminum 5052-H32
Aluminum 5052 excels in corrosion resistance and formability, making it ideal for applications exposed to harsh environments:- Fuel Tanks: Resistant to fuel and corrosion.
- Decking: Provides durability and resistance to weather.
- Roofing Materials: Protects against the elements while being lightweight.
- Enclosures: Safeguards equipment from environmental damage.
- Kitchenware and Food Cans: Offers hygiene and resistance to acids and corrosion.
- Aluminum 6082-T6
Similar to 6061 but with higher strength, Aluminum 6082 is used where additional durability is required:- Construction: Used in bridges, towers, and structural components for its strength.
- Heavy-Duty Machinery: Supports robust machinery and equipment.
- General Engineering: Preferred for applications needing strong, corrosion-resistant materials.
- Aluminum 7075-T6
Known for its high strength and fatigue resistance, 7075 is ideal for high-stress applications, especially in aerospace and military sectors:- Aircraft Frames: Provides the strength needed for structural integrity.
- Military Parts: Used in components requiring exceptional toughness.
- Motorcycle Frames: Offers strength and reduced weight.
- High-Performance Sports Equipment: Includes parts for bicycles and climbing gear.
- Aluminum 6061-T6
A versatile and popular aluminum alloy, 6061-T6 is well-regarded for its machinability and overall mechanical properties:- Automotive Parts: Ideal for chassis and other structural components.
- Bicycle Frames: Lightweight and strong for performance.
- Valves and Computer Parts: Used in a range of industries for precision components.
- Aluminum 2024-T4
Offering moderate to high strength, Aluminum 2024-T4 is suitable for applications requiring good fatigue resistance:- Aircraft Fuselage: Provides high strength for aircraft structures.
- Vehicle Parts: Used in components requiring strength and toughness.
- Wing Tension Members: Supports structural integrity under stress.
- Aluminum MIC 6
Aluminum MIC 6 is notable for its stability and precision, thanks to its unique alloy composition and casting method:- Machining Components: Offers high accuracy and machinability.
- Electronics: Used in precision parts.
- Laser Technology: Ensures stable performance in high-tech applications.
- Aluminum 6082
This grade offers higher strength compared to 6061 and is known for its excellent corrosion resistance:- Construction: Suitable for bridges, towers, and other heavy-duty structures.
- General Engineering: Ideal for applications requiring enhanced strength and toughness.
Conclusion Aluminum’s combination of machinability, strength, corrosion resistance, and recyclability makes it an excellent material for CNC machining. Its adaptability to complex designs and performance in various conditions further solidify its position as a preferred choice in many industries. By selecting the right aluminum grade, you ensure optimal performance and durability for your applications.
Why Choose Our Aluminum CNC Machining Services?
As discussed, aluminum’s exceptional machinability and versatility make it a preferred choice for various applications. When selecting a provider for your aluminum CNC machining needs, it’s crucial to partner with a company that not only leverages these advantages but also brings extensive experience to the table.
At [Your Company Name], we specialize in aluminum CNC machining, bringing over a decade of experience in working with a wide range of aluminum grades, including commonly used alloys such as 6061, 2024, and 5052. Our state-of-the-art equipment and industry expertise ensure precision and efficiency for both prototyping and full-scale production.
Here’s what sets us apart:
- Expertise: Extensive experience in machining a variety of aluminum grades to meet diverse requirements.
- Quality: Consistent delivery of high-quality results with tight tolerances and minimal rework.
- Efficiency: Streamlined production processes that reduce lead times and enhance overall efficiency.
- Cost Savings: Long-term savings achieved through precise machining and reduced waste.
- Customer Satisfaction: A commitment to exceeding your expectations with customized solutions and exceptional service.
By choosing our aluminum CNC machining services, you benefit from our deep expertise in handling commonly used aluminum alloys and our dedication to delivering top-notch results. Let us support your projects with precision and efficiency that make a difference.