Aluminium machining
We specialize in aluminium machining, offering CNC milling, turning, and other services. Get high-quality custom aluminium parts made to your exact specifications. Contact our experts today!
Prototeque: Your Trusted Aluminium machining Partner In China
Prototeque is a seasoned machining parts manufacturer with a decade of expertise delivering precision aluminium components. We specialize in cnc turning parts and cnc milling parts, catering to a wide range of industries.
Our advanced machinery, including 3 axis cnc milling machine, 4 axis cnc milling machine, 5 axis cnc machining, and cnc turning milling machine, enables us to handle intricate complex cnc machining projects with unparalleled precision. Whether you need a single one off cnc machining prototype or high quantities for high volume cnc machining, we’ve got you covered.
From minuscule small machined parts to substantial large part machining, our capabilities are extensive. We excel in small batch cnc machining and can adapt to your specific requirements. Trust Protoeque for all your aluminium machining needs.
Common Aluminium Alloys for CNC Machining
Choosing the right cnc material for your project is crucial for its success. Aluminium alloys are a popular choice due to their versatility, lightweight properties, and excellent machinability. As experts in aluminium CNC machining,we’ve accumulated extensive experience working with these aluminium alloys. Our in-depth knowledge allows us to deliver precision components tailored to your exact specifications.We specialize in:
6061-T6 Aluminium
6063-T6 Aluminium
6082-T6 Aluminium
7075-T6 Aluminium
Common Surface Finishes for CNC Aluminium Parts
We offer a range of surface finishes to enhance both aesthetics and functionality, providing optimal protection against corrosion. Our anodizing processes exceed industry standards, with many finishes passing rigorous salt spray tests of 72 hours or more.
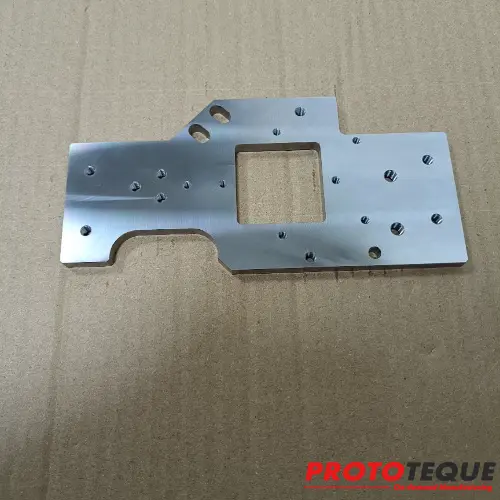
Machined + Anodized: Combines precision machining with a durable, corrosion-resistant anodized coating for a sleek and professional look.
Brushed + Anodized: Creates a sophisticated matte finish with the added benefits of anodizing.
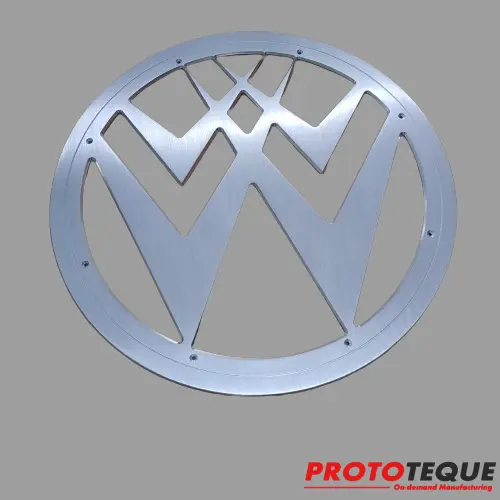
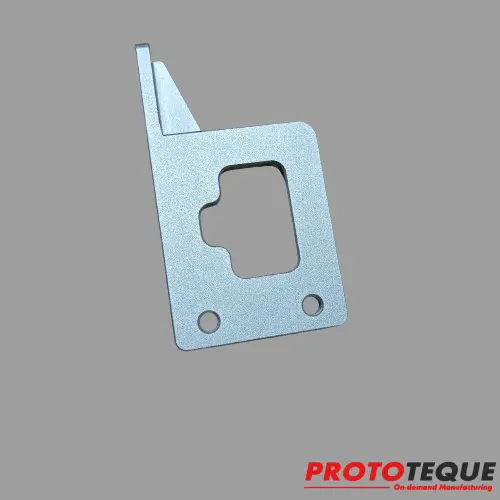
Sandblasted + Anodized: Provides a textured surface with enhanced durability and corrosion protection.
Hard Anodized: Delivers exceptional hardness, wear resistance, and corrosion protection. While typically available in black, it offers superior durability compared to standard anodizing.
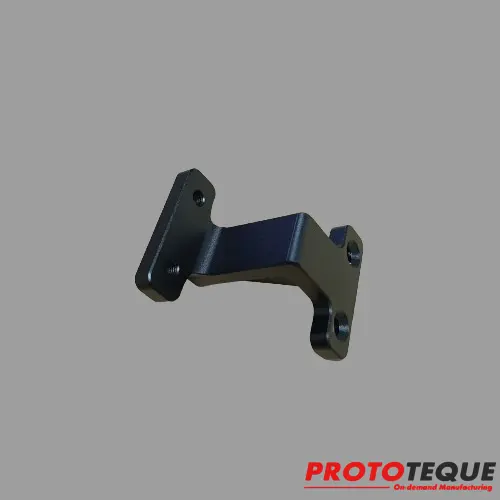
Your questions answered
Common questions
What factors affect the price of an aluminium machined part?
Several factors influence the price of an aluminum machined part. These include:
Dimensional tolerances: Tighter tolerances require more precise machining, increasing cost.
Surface finish: A finer surface finish (lower Ra value) generally demands additional processing steps, impacting price.
Part complexity: Features such as small radii (R less than 1mm), internal right angles, or small, long holes can increase machining time and cost.
Hole diameter: Precision machining of small holes (under 1mm) requires specialized tooling, contributing to higher costs.
Small long holes: These features can also increase machining time and cost due to the specialized tooling and processes required.
Can you provide material certificates for your machined aluminum parts?
Yes, we can provide material certificates for all our machined aluminum parts. We source our aluminum raw materials exclusively from leading suppliers known for their high-quality products.
These certificates detail the complete chemical composition of the material and guarantee that all parts are made from virgin aluminum.
What is the difference between hard anodizing and regular anodizing?
Hardness
- Hard Anodizing: Significantly harder than regular anodizing. This increased hardness makes it ideal for applications requiring high wear resistance, such as engine components and molds.
- Regular Anodizing: Less hard compared to hard anodizing. Suitable for decorative purposes and general corrosion protection.
Coating Thickness
- Hard Anodizing: Typically has a thicker coating compared to regular anodizing. This thicker layer provides enhanced protection against wear, corrosion, and abrasion.
- Regular Anodizing: Offers a thinner coating, primarily focusing on aesthetics and basic corrosion resistance.
Unit Price
- Hard Anodizing: Generally more expensive due to the longer processing time and specialized equipment required for the thicker coating.
- Regular Anodizing: Typically more cost-effective compared to hard anodizing.
Anti-Corrosion and Wear Performance
- Hard Anodizing: Offers superior anti-corrosion and wear resistance. Ideal for applications exposed to harsh environments or experiencing high levels of friction.
- Regular Anodizing: Provides good corrosion protection but is not as resistant to wear as hard anodizing.
Color Options
- Hard Anodizing: Primarily limited to dark colors, such as black, due to the thickness of the coating.
- Regular Anodizing: Offers a wider range of color options, including bright and vibrant colors.
What are the different grit options available for brushed and sandblasted finishes?
Grit options for brushed and sandblasted finishes typically range from 80 to 150 grit. The most common grit used for these finishes is 120 grit.
It’s important to note that the higher the grit number, the finer the abrasive, resulting in a smoother surface finish.
However, it’s essential to remember that a higher grit number may not effectively mask defects such as scratches or machining marks.