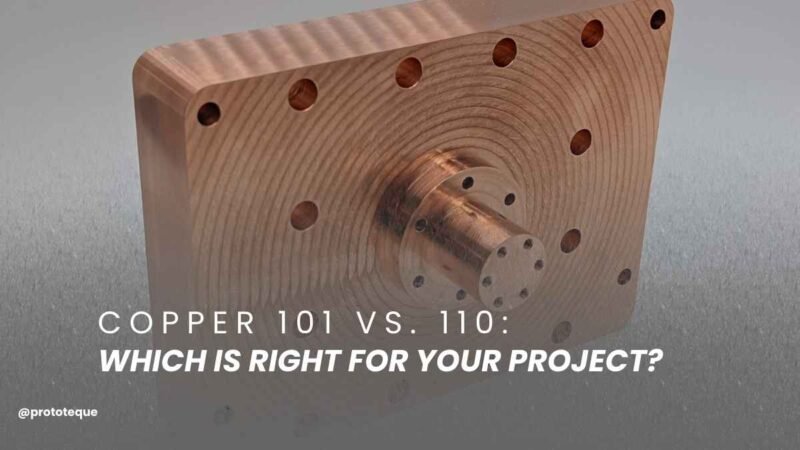
1. Introduction:
Are you in doubt, about whether to choose copper 101 vs 110 for use in your CNC machining project? Since both types possess specific properties designed for a particular use. Substituting the wrong copper alloy may result in low performance, high costs, and sometimes system malfunctions. The absence of a specific structure makes it possible for you to develop a substandard and short-lived product.
When comparing copper 101 vs 110, both are perfect for electrical and thermal applications because of their conductivities. Copper 110 comprised addition of oxygen is stronger and more corrosion-resistant than normal copper. Therefore, it is notably perfect for structural applications and where durability is concerned. This article is all about the distinction between Copper 101 vs 110 concerning their properties, uses, and machined parts, they employ to create.
2. What Is Copper 101?
Copper 101, or C10100, is an oxygen-free, high-conductivity copper type. It has a copper content of at least 99.99 percent. The high purity enables it to be well suited to those areas where the optimum performance in heat transfer and electrical conductivity is desired. Due to these characteristics, it’s considerably the best alloy suitable for demanding systems and electronic parts. Consequently, the high conductivity together with its ability to resist oxidation makes it particularly for precision uses.
2.1. Applications of Copper 101 in CNC Machining
Copper 101 has conformed machining ease. So, it’s preferred in CNC machining over other types of copper. Moreover, the alloy also features a smooth cutting edge and doesn’t cause much wear on the tools as observed with other materials. Therefore, the production of parts that require accurate, high conductivity such as electric connectors, circuit board pads, and terminals is relatively easier. In addition, it excels in making production of intricate feature parts such as soldering tips, heat exchangers, and unique electrical components.
2.2. Components Manufactured from Copper 101:
Here’s a list of typical components, usually made of Copper 101 in many manufacturing industries.
- Electrical Connectors
- Heat Exchangers
- Circuit Board Pads
- Soldering Tips
- Electrical Terminals
- Precision Components
- EMI Shielding Components
- Custom Connectors
- Bus Bars
- Copper Rings
- Copper Strips
2.3. Properties, Chemical Composition, and Machining Options of Copper 101
Category | Property | Details/Figures | Unique Machining Options |
Chemical Composition | Copper (Cu) | 99.99% minimum | Wire EDM: Perfect for high-precise, and intricate geometries such as electrical contacts. |
Oxygen (O) | ≤ 0.02% | Laser Cutting: Ideal for precision cuts in thin-walled parts like heat exchangers. | |
Other Trace Elements | Minimal phosphorus or other trace elements | CNC Milling: Excellent for creating parts like electrical terminals and precision connectors with minimal tool wear. | |
Physical Properties | Density | 8.92 g/cm³ | Precision Turning: Ideal for creating round, cylindrical components such as electrical bus bars. |
Electrical Conductivity | 101% IACS (International Annealed Copper Standard) | Grinding: Essential for fine-tuning the surface finish, particularly in high-end electronic parts. | |
Thermal Conductivity | 390 W/m·K | Polishing: Achieves a high-quality finish without compromising thermal properties, useful for heat exchanger parts. | |
Tensile Strength | 210–250 MPa (Megapascals) | Bending: Suitable for shaping thin copper sheets or custom copper connectors without cracking. | |
Yield Strength | 70–120 MPa | Cold Working: Beneficial for forming copper into more intricate or thin-walled shapes like precision rings. | |
Modulus of Elasticity | 110–130 GPa (Gigapascals) | Stamping: Effective for high-volume manufacturing of parts like circuit board pads and flat connectors. | |
Hardness (Brinell) | 30–50 HB | Cold Rolling: Used for thinning copper to create copper foils or thin-walled parts while maintaining structural integrity. | |
Machinability | Machining Ease | Very easy to machine with minimal tool wear, due to its high purity and ductility. | CNC Milling: Perfect for high-precision, low-tolerance components like heat exchangers, and electrical connectors. |
Surface Finish | Excellent surface finish after machining, providing high-quality, smooth parts. | Laser Cutting: Excellent for precise, clean cuts of complex shapes in thin copper sections. | |
Formability | Very high can be easily formed into custom shapes, wire, sheets, or tubes | Annealing: Relieves stress and increases ductility to allow for complex cold forming and deep drawing. | |
Corrosion Resistance | Corrosion Resistance | Excellent corrosion resistance, especially in non-acidic environments | Electroplating: Helps to intensify surface protection for components exposed to harsh environments. |
Oxidation Resistance | High resistance to oxidation, even when exposed to air over long periods | Surface Coating: Can be coated with Nickel or tin to further protect against oxidation in outdoor or humid conditions. | |
Temperature Stability | Maximum Operating Temperature | Up to 200°C (degrees Celsius) without significant degradation. | Heat Treatment: It can be used to soften Copper 101 for easier machining or to restore ductility after heavy work. |
3. What Is Copper 110?
Copper 110 or C11000, has approximately 99.9% of copper and 0.02% oxygen. The slight addition of oxygen further signifies the tensile strength of the copper material and retains good chemical and physical conductivity, simultaneously. Copper 110 is particularly famous for its ductility, and can be bent, shaped, or formed. Moreover, it’s relatively less susceptible to embrittlement than other copper alloys while the corrosion resistance of the alloy makes it suitable for use both indoors and outdoors applications.
3.1. Properties, Chemical Composition, and Machining Options of Copper 110
Category | Property | Details/Figures | Unique Machining Options |
Chemical Composition | Copper (Cu) | 99.9% minimum | Wire EDM: Ideal for intricate cuts in thin copper sections without generating heat. |
Oxygen (O) | ≤ 0.02% | Laser Cutting: Excellent for clean, precise cuts, especially for complex shapes. | |
Other Trace Elements | Minor traces of phosphorus, lead (for machinability), and other impurities. | CNC Milling: Enables precise machining of components with minimal tool wear. | |
Physical Properties | Density | 8.96 g/cm³ | Turning and Drilling: Best for creating cylindrical or round shapes while maintaining tight tolerances. |
Electrical Conductivity | 98% IACS (International Annealed Copper Standard) | Electroforming: Used for high-precision, intricate parts where high conductivity is crucial, such as connectors and terminals. | |
Thermal Conductivity | 401 W/m·K | Polishing: Provides a mirror finish to components where heat dissipation is critical, such as in cooling systems or radiators. | |
Tensile Strength | 210–310 MPa (Megapascals) | Brazing: Used for joining parts, providing strong, long-lasting bonds without compromising the material’s conductivity. | |
Yield Strength | 70–150 MPa | Hot Working: Ideal for larger components that require shaping and bending without cracking, like bus bars. | |
Modulus of Elasticity | 110–130 GPa (Gigapascals) | Cold Working: Works well for shaping Copper 110 into complex parts, such as thin sheets or intricate shapes. | |
Hardness (Brinell) | 30–60 HB | Grinding: Used for maintaining a smooth finish on high-precision copper components, especially in electrical or high-performance parts. | |
Machinability | Machining Ease | Extremely easy to machine with minimal tool wear due to its high ductility and malleability. | High-Speed CNC Milling: Offers excellent precision for mass production of electrical connectors, terminals, and bus bars. |
Surface Finish | Achieves excellent surface finishes, ideal for high-quality appearance in electronics or decorative applications. | Wire EDM: Produces smooth, fine-cut edges without the thermal distortions that affect other methods like laser or plasma cutting. | |
Formability | Very good, and can be cold-formed into shapes like wire, sheets, and strips. | Stamping: Effective for mass production of flat or formed copper parts such as electrical terminals or connectors. | |
Corrosion Resistance | Corrosion Resistance | Highly resistant to corrosion, especially in fresh water and atmospheric environments. | Surface Treatment: Nickel Plating or Phosphating can be applied to improve corrosion resistance in harsh environments. |
Oxidation Resistance | Maintains surface integrity even when exposed to air for extended periods. | Electroplating: Enhances oxidation resistance and increases the durability of the surface in environments with high humidity or salt. | |
Temperature Stability | Maximum Operating Temperature | Suitable for use in temperatures up to 200°C without significant degradation of mechanical properties. | Annealing: Used to relieve stress and improve the workability of Copper 110 in complex parts, particularly for heat exchangers. |
4. Prototeque: Precision Copper CNC Machining Service
Are you looking for copper CNC machining services? Prototeque got you. We offer high-quality Copper 101 (C10100), Copper 110 (C11000), and other copper alloy part fabrication services to suit a variety of projects. As an ISO 9001:We are the certified provider of 2015 and employ modern technologies to produce and supply the best parts at reasonable prices.
Our skilled engineers ensure your Design for Manufacture (DFM) is reviewed to choose the right copper alloy and manufacturing techniques for your application. We help with improving product quality, changing components, and selecting the right surface finishing treatment to suit your requirements.
So, why wait, Submit your CAD file today to get the CNC price quote in minutes and a DFM overview in no time.
5. Conclusion: The Right Choice between Copper 110 vs 101
To sum up, the ultimate choice between Copper 101 vs 110, entirely depends on your project requirements. For applications where electrical conductivity is crucial, you can utilize Copper 101 can be optimal. Since it serves well on high-performance parts/products. However, if your project needs better mechanical characteristics and non-corrosion abilities, Copper 110 is an all-around product for your projects due to its peculiar strength, durability, and conductivity.