Stainless Steel CNC Machining
We specialize in precision stainless steel CNC machining. Our expertise includes milling, turning, and other processes to create custom parts that meet your exact specifications. Benefit from our high-quality stainless steel components, ideal for demanding applications. Contact us for a quote today.
Prototeque: Your Trusted Stainless Steel CNC Machining Partner
Prototeque is a leading CNC machining manufacturer specializing in precision stainless steel components. With a decade of expertise, we deliver high-quality custom parts tailored to your exact specifications.
Our state-of-the-art facilities, including 3-axis and 5-axis CNC machining centers, enable us to handle complex stainless steel projects with unmatched precision.
Whether you need a single prototype or high-volume production, we offer reliable stainless steel CNC machining services. Trust Protoeque for all your stainless steel component needs.
Prototeque: Common Stainless Steel for CNC Machining
Stainless steel is the material of choice for demanding applications due to its exceptional strength, durability, and corrosion resistance. At Prototeque, we specialize in transforming stainless steel into precision metal machined parts that meet the highest standards. Our expertise in stainless steel CNC machining allows us to deliver custom metal components tailored to your exact specifications.
SS Grade 17-4 (PH Stainless Steel)
SS304 (Stainless Steel)
316L Stainless Steel
SS416 (Stainless Steel)
Stainless Steel 18-8
Stainless Steel 303
Prototeque: Common Surface Finishes for stainless steel cnc parts.
Enhance the look and performance of your stainless steel CNC parts with Prototeque’s expert surface finishing services. Our wide range of finishes, from polished stainless steel milling parts to custom-finished turned components, combine aesthetics with durability, providing optimal protection against corrosion.
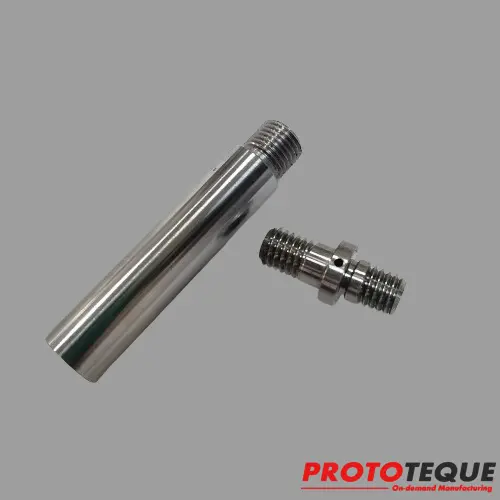
As-Machined Finish
- The raw, untreated surface condition of CNC machined parts. It retains the original tool marks and imperfections from the machining process.
- Common Ra values for as-machined parts range from Ra 0.4 to Ra 3.2, depending on the machining process and desired tolerances.
Brushed Finish
- A mechanical process that creates a linear or circular pattern on the surface of CNC machined components using abrasive materials.
- Appearance: Matte or satin finish with a consistent, directional pattern.
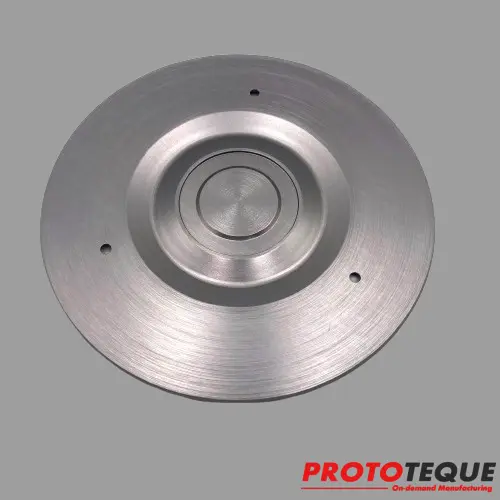
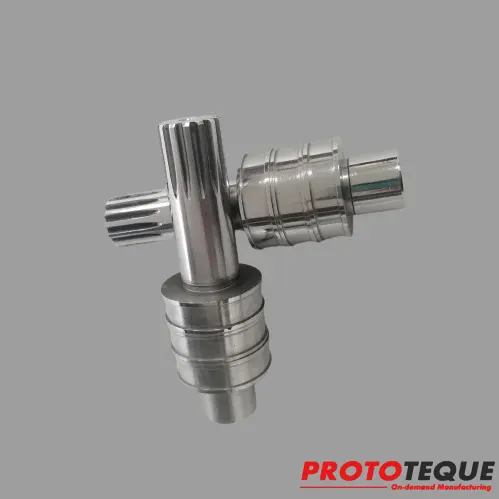
Polished Finish
- A process that removes surface imperfections and creates a smooth, reflective surface on CNC machined parts through abrasive techniques.
- Appearance: Smooth, shiny, and mirror-like finish.
Passivation
- A chemical process that removes iron contaminants from the surface of stainless steel CNC machined parts, enhancing its corrosion resistance.
- Appearance: Does not alter the visual appearance but improves the metal’s resistance to corrosion.
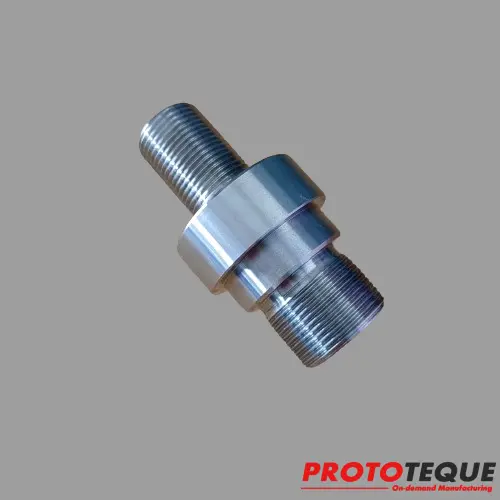
Your questions answered
Common questions
What stainless steel is magnetic?
Magnetism in Stainless Steel
Not all stainless steel grades are magnetic. The magnetic properties of stainless steel primarily depend on its crystal structure.
Austenitic stainless steels, such as 303, 304, and 316, have a non-magnetic crystal structure.
On the other hand, ferritic and martensitic stainless steels, including 17-4 PH, 18-8 (which is typically a 300 series stainless steel), and 416, are magnetic.
which stainless steel is best
There’s no definitive “best” stainless steel for all applications. The optimal choice depends on a variety of factors specific to your project, including:
Corrosion resistance: Will the part be exposed to harsh environments or chemicals?
Strength and durability: What level of stress will the part endure?
Machinability: How easily do you need to process the material?
Cost: What is your budget for the material?
Common Stainless Steel Grades and Their Characteristics
To help you make an informed decision, let’s briefly compare some common stainless steel grades:
SS304: Versatile, good corrosion resistance, widely used.
316L: Superior corrosion resistance, especially in chloride environments.
17-4 PH: High strength, heat treatable for increased hardness.
SS416: Excellent machinability, good corrosion resistance.
Remember: This is a simplified overview. Each grade has specific variations and properties that might influence your choice.
Is 304 stainless steel machinable?
Yes,
304 stainless steel is generally considered machinable. However, its machinability can vary depending on the specific machining process and the desired tolerances.
Factors Affecting Machinability of 304 Stainless Steel
Work hardening: 304 stainless steel has a tendency to work harden during machining, which can lead to tool wear and increased cutting forces.
Heat generation: Machining stainless steel generates heat, which can further contribute to work hardening and tool wear.
Chip formation: The formation of long, continuous chips can hinder machining efficiency and increase the risk of tool breakage.
Machinability Compared to Other Materials
While 304 stainless steel is generally machinable, it is less machinable than some aluminum alloys like 6061. Aluminum alloys tend to be softer and have better chip removal properties.
To optimize the machining of 304 stainless steel, it’s essential to use appropriate cutting tools, cutting parameters, and cooling techniques.
Is 316L easier to machine than 304?
Yes
304 vs. 316L Stainless Steel: Machinability and Deformation
Machinability:
316L is generally easier to machine than 304 stainless steel.
304 stainless steel is more prone to work hardening and tool sticking during machining, making it more challenging to cut.
Deformation:
304 stainless steel is more susceptible to deformation after machining due to its lower strength and higher ductility.
316L is more resistant to deformation due to its higher strength and hardness.
It’s important to note that these are general trends and the specific behavior of the materials can vary depending on factors like machining conditions, heat treatment, and final part geometry.
What is the heat treatment process for 17-4 PH stainless steel?
17-4 PH stainless steel is renowned for its exceptional combination of high strength, corrosion resistance, and toughness. Its heat treatment process involves several stages to achieve desired properties.
Basic Heat Treatment Stages for 17-4 PH
Solution Treatment: Heating to a specific temperature (typically 1750-1900°F or 955-1038°C) to dissolve carbides and other precipitates, followed by rapid quenching to retain the austenitic structure.
Precipitation Hardening: Aging at a lower temperature (typically 900-1150°F or 482-621°C) to form fine precipitates, increasing strength and hardness. Multiple aging steps can be used for different property combinations.
Common Heat Treatment Cycles
The specific heat treatment cycle for 17-4 PH depends on the desired mechanical properties. Common cycles include:
H900: Good combination of strength and toughness.
H1025: Higher strength than H900 but with slightly reduced toughness.
H1050: Highest strength condition, but with lower ductility and toughness.
H1100: Maximum corrosion resistance.
Additional Considerations
Cooling Rate: Affects microstructure and properties.
Aging Time and Temperature: Determine precipitate formation, influencing strength, hardness, and ductility.
Stress Relief: May be required to reduce residual stresses.
Machining: Due to potential deformation after heat treatment, machining 17-4 PH often involves a two-step process: coarse machining before heat treatment and fine machining afterwards to achieve precise dimensions and tolerances.