Steel CNC Machining
Expert steel CNC machining, milling, and turning services. Precision-crafted custom metal parts. Reliable machining manufacturers. Bring your steel project to life with us.
Prototeque: Your Precision Steel Machining Partner in China
Prototeque is a leading manufacturer of high-precision steel components. With a decade of experience in metal CNC machining, we excel at delivering custom steel parts tailored to your exact specifications. Our expertise in 3-axis and 5-axis CNC milling ensures exceptional accuracy and surface finish for even the most complex steel machining projects.
From small-scale prototypes to large-volume production runs, we offer comprehensive steel CNC machining services. Our state-of-the-art equipment and skilled technicians guarantee superior quality and timely delivery. Whether you require simple or intricate steel parts, trust Protoeque to exceed your expectations.
Prototeque: Common Steels Alloys and Carbon Steels for CNC Machining
Selecting the ideal cnc machining metal is crucial for project success. Steel, renowned for its strength and durability, is a prime choice across diverse industries. As experts in steel CNC machining, we leverage our in-depth knowledge to deliver precision machined parts tailored to your exact specifications. Our expertise lies in transforming steel into high-quality components that meet your project’s unique demands.We specialize in:
AISI/SAE 1080: High carbon steel
AISI/SAE 1020: Mild steel
AISI/SAE 4140: Chromium-molybdenum alloy steel
AISI/SAE 1018 Mild Steel
AISI/SAE 4340
Common Surface Finishes for CNC Steel Parts
Enhance the look and life of your steel components with our range of premium surface finishes. We offer a variety of treatments to protect against corrosion, improve durability, and enhance aesthetics. Our common surface finishes include:
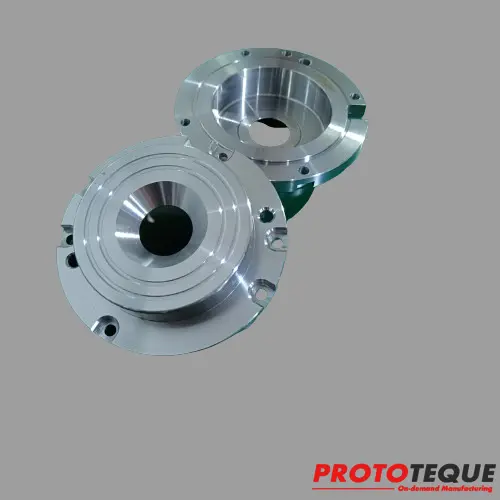
As Machined + Hard Chrome plating
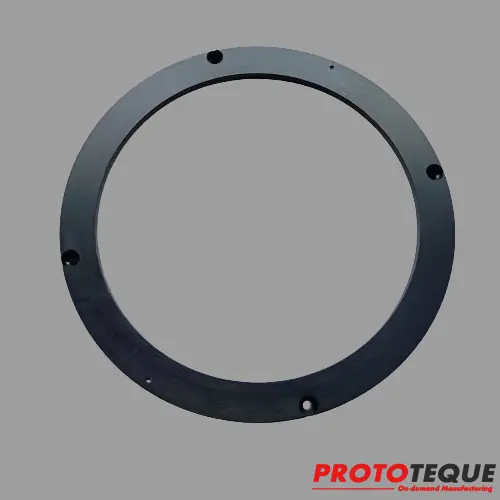
Black oxide
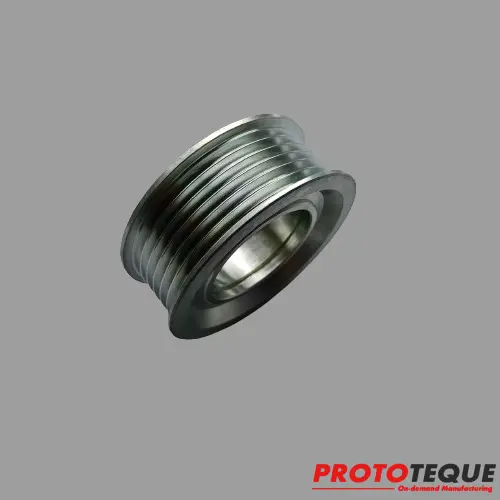
Zinc Plating
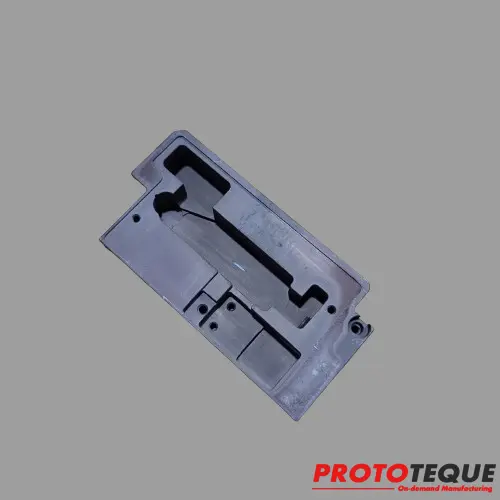
Heat treatment
Your questions answered
Common questions
Do you offer finishing options for steel CNC machined parts?
Yes, we offer a wide range of finishing options to enhance the appearance, durability, and functionality of your steel CNC machined parts. Our services include:
Protective Coatings: Powder coating, electrophoresis, zinc plating, chrome plating, nickel plating, and painting.
Surface Enhancement: Black oxide, nitriding, and carburizing.
Welding: For joining multiple parts or repairing defects.
Other Finishes: Phosphating and PVD coatings.
We can tailor our finishing process to meet your specific requirements.
Steel CNC Machining VS Metal 3D Printing
Choosing between steel CNC machining and metal 3D printing depends on a variety of factors. Both processes have their own strengths and limitations.
Steel CNC Machining
Ideal for: Simple to moderately complex parts requiring high precision, tight tolerances, and excellent surface finish.
Advantages: Typically faster production times for larger quantities, lower cost per part, superior dimensional accuracy, and a wider range of material options.
Limitations: Less suitable for highly complex internal structures or intricate geometries.
Metal 3D Printing
Ideal for: Complex parts with intricate geometries, low-volume production, and rapid prototyping.
Advantages: Ability to create complex shapes, no tooling required, potential for lightweight designs.
Limitations: Generally slower production times, higher cost per part, limitations in material options, and often requires post-processing for optimal surface finish and mechanical properties.
In many cases, a combination of both processes can be beneficial. For instance, metal 3D printing can be used to create a complex mold or pattern, which can then be used for CNC machining to produce final parts with high precision and accuracy.
Ultimately, the best choice depends on specific project requirements. Factors such as part complexity, quantity, material selection, budget, and lead time should be carefully considered when making a decision.
Steel CNC Machining VS Metal Injection Molding (MIM)
Steel CNC machining and metal injection molding (MIM) are both effective methods for producing metal parts, each with its own strengths and limitations.
Steel CNC Machining: Offers flexibility in design and material choice, making it ideal for rapid prototyping, low to medium volume production, and parts requiring high precision and tight tolerances. While unit costs are higher compared to MIM for high volumes, there’s no upfront tooling cost.
Metal Injection Molding (MIM): Excels in producing complex, small-to-medium-sized parts in high volumes. MIM offers lower unit costs for large quantities due to tooling amortization. However, there’s a significant upfront investment in tooling. MIM also has limitations in terms of part size, material options, and strength compared to some steel alloys. A unique advantage of MIM is the ability to insert different metal alloys into the mold, creating hybrid parts.
Key Differences:
Feature | Steel CNC Machining | Metal Injection Molding (MIM) |
Unit Cost | Higher for lower volumes | Lower for high volumes |
Tooling Cost | Low | High |
Lead Time | Short | Longer due to tooling |
Part Complexity | Suitable for simple to moderately complex parts | Ideal for complex parts with intricate details |
Material Options | Wide range of steel alloys | Limited metal options, but allows for inserts |
Part Size | Versatile | Limitations on minimum and maximum part size |
Material Waste | Higher due to material removal | Minimal waste |
Strength | Generally higher for some steel alloys | Lower density can impact strength in some cases |
What is the most common steel for machining?
The most common steel for machining is mild steel. It’s often referred to as 1018 steel or AISI 1018.